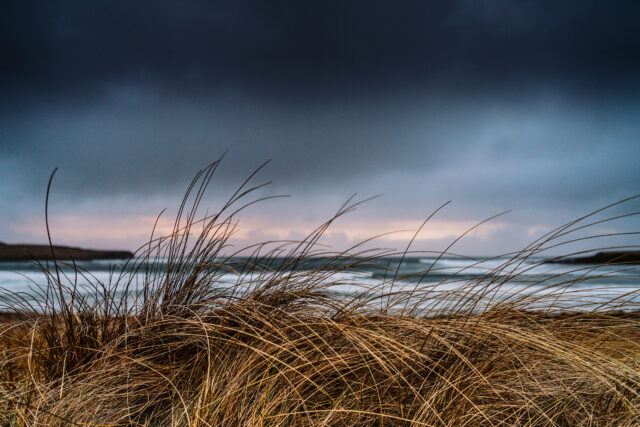
Adapting to a changing climate
The changing climate is affecting all forms of farming and salmon farming is no exception.
When it comes to carbon footprint, it's thought that salmon has one of the lowest of the livestock farming sectors.
We’re also working hard at company level to explore ways we can reduce our carbon footprint even further: from freshwater and marine farming through to processing, packing and logistics.
We’ve been working with UK retailers to help reduce the use of plastics by replacing expanded polystyrene (EPS) packaging with returnable, re-usable ‘bulk bins’ wherever possible.
EPS has long been the preferred packaging solution for transporting perishable food produce such as fruit, meat and fish, owing to its lightweight insulating properties which preserve temperature and, in turn, food quality and safety.
However, as a single-use packaging solution with limited options for recycling, EPS is not without its environmental footprint, prompting us to seek a more footprint-friendly alternative.
Over 40 prototypes later, we finally found our solution: bulk bins. Not only can they be returned by retail customers for re-use, but they also require less ice and energy compared with transporting the same volume of fish via EPS packaging.
Wherever our salmon is headed – domestic market or export customer – it first has to be transported by road.
Working in close collaboration with our logistics partners, we’ve introduced new ways to make the most efficient use of these road miles.
This includes working with Northwards to custom-build a whole new type of trailer, the Insuliner, which has made it possible to transport fresh salmon to market then use the return leg to transport fish feed, significantly reducing the number of ‘empty’ miles.
The Insuliner has also removed the need for wooden pallets and flat racks, reducing our footprint further.
What about air miles?
With regards to air miles, nearly half of all Scottish farmed salmon – the UK’s biggest seafood export – is now transported in the lower belly of regular passenger planes, as opposed to freight-only planes, helping make best use of long-haul flights that are already scheduled.
Indeed, in the BBC Two programme ‘What Britain buys and sells in a day’, presenter Ed Balls learns that roughly 90 per cent of the cargo that goes through Heathrow Airport goes on passenger planes, ranging from pharmaceuticals to aircraft engines.
You can watch a clip from the programme here.
By investing across our freshwater, marine farming and processing facilities, we’re now able to repurpose what would otherwise be considered waste products into valuable by-products.
This includes:
Freshwater
Marine
Processing
It’s all part of our ongoing drive to derive maximum use and value from the salmon we grow and minimise any waste.
From what energy sources we use to how much energy we use, we’re making a conscious effort to go greener.
Freshwater
Much of the heat and hot water at our 17,500 sqm Barcaldine Hatchery is provided by a 600kw biomass energy system.
Supplied, installed and maintained by AMP Clean Energy, it uses locally sourced, sustainably managed wood chip, saving 683 tonnes of carbon annually compared with oil. That’s the equivalent of six million road miles by car.
Other greener approaches at the same facility include:
Marine
In 2020, we embarked on our first trial of hybrid battery power to reduce fuel consumption, carbon emission and operating costs on our marine farms.
Working alongside the conventional diesel generator, the hybrid battery system intelligently monitors power demand, switching seamlessly between generator power and battery power.
At times of greater demand such as during feeding, power is handed back to the generator which simultaneously charges the hybrid’s batteries. During lower demand, the hybrid takes over, remaining on 24/7 to power comparatively low loads such as environmental loggings systems.
In its first full 12 months in operation, the system successfully saved 31,488 litres of diesel and 83,128 kg of CO₂.
You can watch our short animation of how the hybrid battery system works here.
Complementing this work, we’ve also introduced a new greenhouse gas app to provide insights on where we could make further energy savings.
Created by our own in-house IT team, the app enables us to see what energy we are using per farm, per region and per year. Once a farm has harvested an entire crop, we will also be able to work out its carbon footprint per tonne of salmon produced.
Processing
At our South Shian processing facility on Scottish mainland we have installed wireless sensor technology, created by the same in-house IT team as our greenhouse app, to accurately measure the volume of water and electricity being used and help identify where greater efficiencies could be made.
On the remote Orkney island of Eday, we’ve helped build staff and visitor accommodation featuring:
You can read more about this project here.